When working on woodworking projects, one crucial factor to consider is whether to use air dried or kiln dried lumber. Since the drying method plays a significant role in determining the wood’s moisture levels, stability, and overall quality.
As every woodworker knows, two common methods of drying lumber are air drying and kiln drying, each with its own set of advantages and disadvantages.
In order to choose the right option for your project, you will need to learn about the differences between air-dried and kiln-dried lumber as well as their characteristics and applications.
Table of Contents
Why Does Wood Have to Be Dried Before Use?
Wood is a porous material that absorbs and releases moisture depending on its environment. If wood with a high moisture content is used in dry conditions or outdoors where the moisture level is relatively lower, it will try to adjust by releasing moisture. This causes the wood to shrink.
If the moisture content of the wood is very high when used, it may release a lot of moisture and shrink considerably, potentially changing its shape or appearance and impacting the quality of the project.
Drying wood before use ensures that the moisture content is at an appropriate level so that it does not undergo excessive shrinking or expanding by absorbing or releasing moisture when exposed to different environments.
What Is the Ideal Moisture Content of Wood?
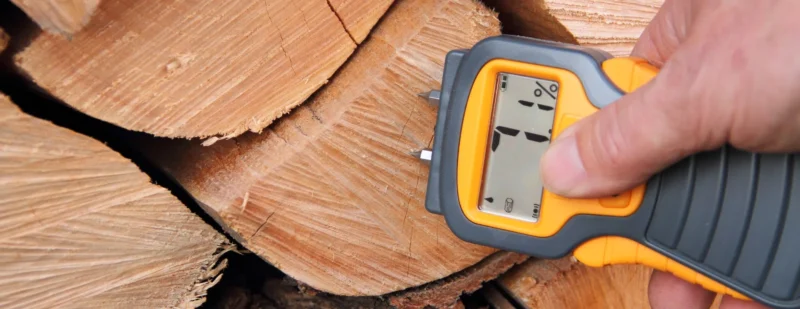
The ideal moisture content varies depending on the intended use and the environmental conditions where the wood will be utilized.
For indoor projects, a moisture content between 6% and 8% is recommended, while outdoor projects may require a slightly higher range of 9% to 14%.
Similar to indoor furniture, wood flooring should have a moisture content from 6% to 9% to match the indoor environment to maintain stability and ensure a long-lasting installation.
How to Dry Wood?
There are many ways to dry wood to reduce its moisture content, but the most common wood drying methods used commercially are air dried and kiln dried. We’ll explain these methods below as well as discuss the various differences between them.
Air-Dried Wood |
Kiln-Dried Wood |
|
Method of Drying | Natural process, wood stacked with spacers, dried by air | Controlled process in a kiln with regulated temperature, humidity, and airflow |
Moisture Content | Typically 12-15% | Typically 6-8% |
Drying Time | Several months to a few years | A few days to a few weeks |
Stability | More prone to moisture-related changes | More stable due to lower, consistent moisture content |
Cost | Generally less expensive due to lack of specialized equipment | More expensive due to energy and equipment costs |
Natural Color | Retains more natural color and texture | May lose some natural color due to high temperatures |
Yield and Quality | Higher risk of defects, decay, and loss | Higher quality and yield, fewer defects due to controlled drying |
Best Use | Outdoor projects, rustic furniture | Indoor furniture, cabinetry, flooring, commercial manufacturing |
Air dried, also known as natural drying, is a time-honored method of reducing the moisture content in lumber. The lumber is left in the open air, exposed to natural environmental conditions, for an extended period to reach a certain moisture content.
Kiln dried is a more advanced and controlled method of reducing the moisture content in lumber. This process involves placing the wood in a specialized chamber, called a kiln, where temperature, humidity, and airflow are carefully regulated to achieve efficient and consistent drying.
Process of Air dried & Kiln Dried
Air-dried is a natural process where lumber is stacked in layers with spacers (stickers) between each board to allow for air circulation. The stacks are typically placed in a dry, shaded area with good ventilation. This method relies on the ambient conditions of the environment to slowly reduce the moisture content of the wood over time. The process can be heavily influenced by weather conditions, requiring months or even years to achieve the desired moisture content. For example, air-drying thick oak lumber can take up to 2 years in some regions.
In contrast, kiln-drying involves placing lumber in a large oven-like kiln where temperature, humidity, and airflow are carefully controlled. This method allows for precise regulation of the drying environment, enabling a much faster reduction in moisture content. Kiln-drying can be completed within days or weeks, making it a much quicker alternative to air-drying.
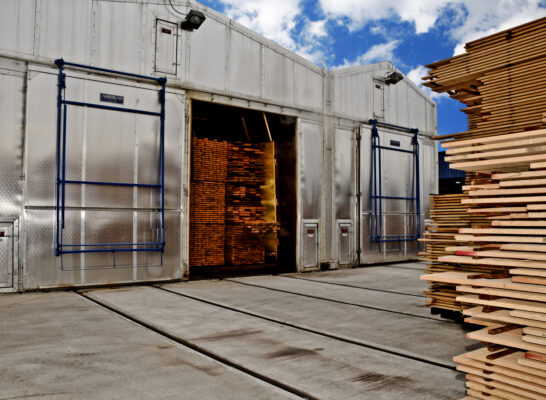
Stability
Stability refers to the wood’s ability to maintain its dimensions and structural integrity over time. Air-dried lumber, with its higher moisture content, can be more susceptible to changes in environmental humidity, leading to potential issues like warping, twisting, or cracking.
Kiln-dried lumber, with its lower and more consistent moisture content, offers superior stability. The controlled drying process reduces internal stresses and minimizes the risk of dimensional changes. This makes kiln-dried wood an excellent choice for applications where exact measurements and long-term stability are essential, such as in cabinetry, flooring, and fine furniture.
Drying Time
The drying time for air-dried lumber can be extensive. It can take several months to a few years to reach the desired moisture content.
Kiln-drying significantly shortens the drying time to a few days or weeks. The accelerated process allows manufacturers and builders to maintain a steady supply of dry lumber, ensuring that projects can proceed without lengthy delays. A commercial kiln can typically dry a charge of 1-inch thick hardwood lumber to 6-8% moisture content within 10-14 days.
Cost
One of the primary advantages of air dried is its cost-effectiveness. Since it relies solely on natural air circulation, there are no energy or machinery costs involved.
Kiln dried, on the other hand, does come with a higher cost due to the energy-intensive nature of the process and the specialized equipment required. Estimates suggest that kiln dried can cost 2-3 times more than air dried per board foot of lumber.
The higher initial cost is often justified by the improved quality and faster availability of the dried lumber. For many commercial operations, the ability to quickly supply large quantities of stable, dry wood outweighs the additional expense.
Uses
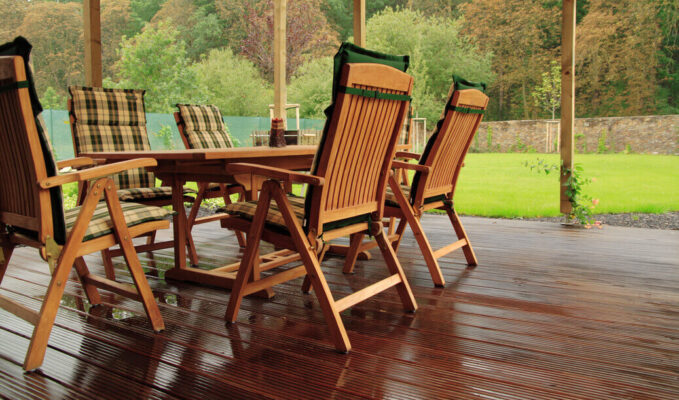
Air-dried lumber is well-suited for outdoor projects, rustic furniture, and budget-conscious applications where the natural look of the wood is preferred, and slight dimensional changes are acceptable.
Kiln-dried lumber is usually the go-to choice for indoor furniture, cabinetry, flooring, and commercial manufacturing. Its superior stability, lower moisture content, and consistent quality make it ideal for precision work and applications where long-term performance and aesthetic appeal are crucial.
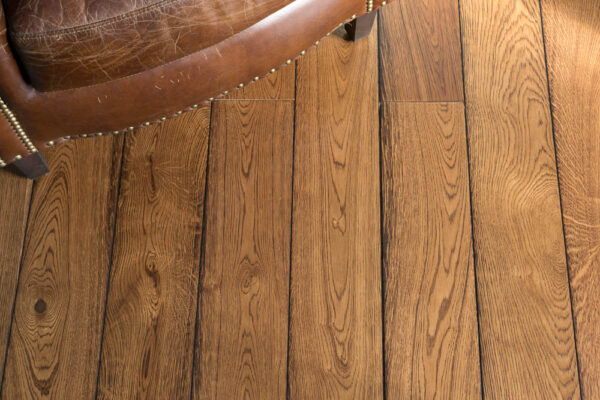
In conclusion, the choice between air-dried and kiln-dried lumber depends on the specific requirements of your project, including budget, time constraints, and personal preferences. By considering these factors and consulting with reputable lumber suppliers, you can ensure that you select the most appropriate drying method for your woodworking needs, enabling you to create beautiful and long-lasting projects.
At K-Timber, we offer both options for our customers to decide what’s fit for their projects. From high quality air dried wood with moisture content below 20% to kiln dried from between 9% – 12%, we are confident to provide the best services and quality to our customers. Contact us to know more.